
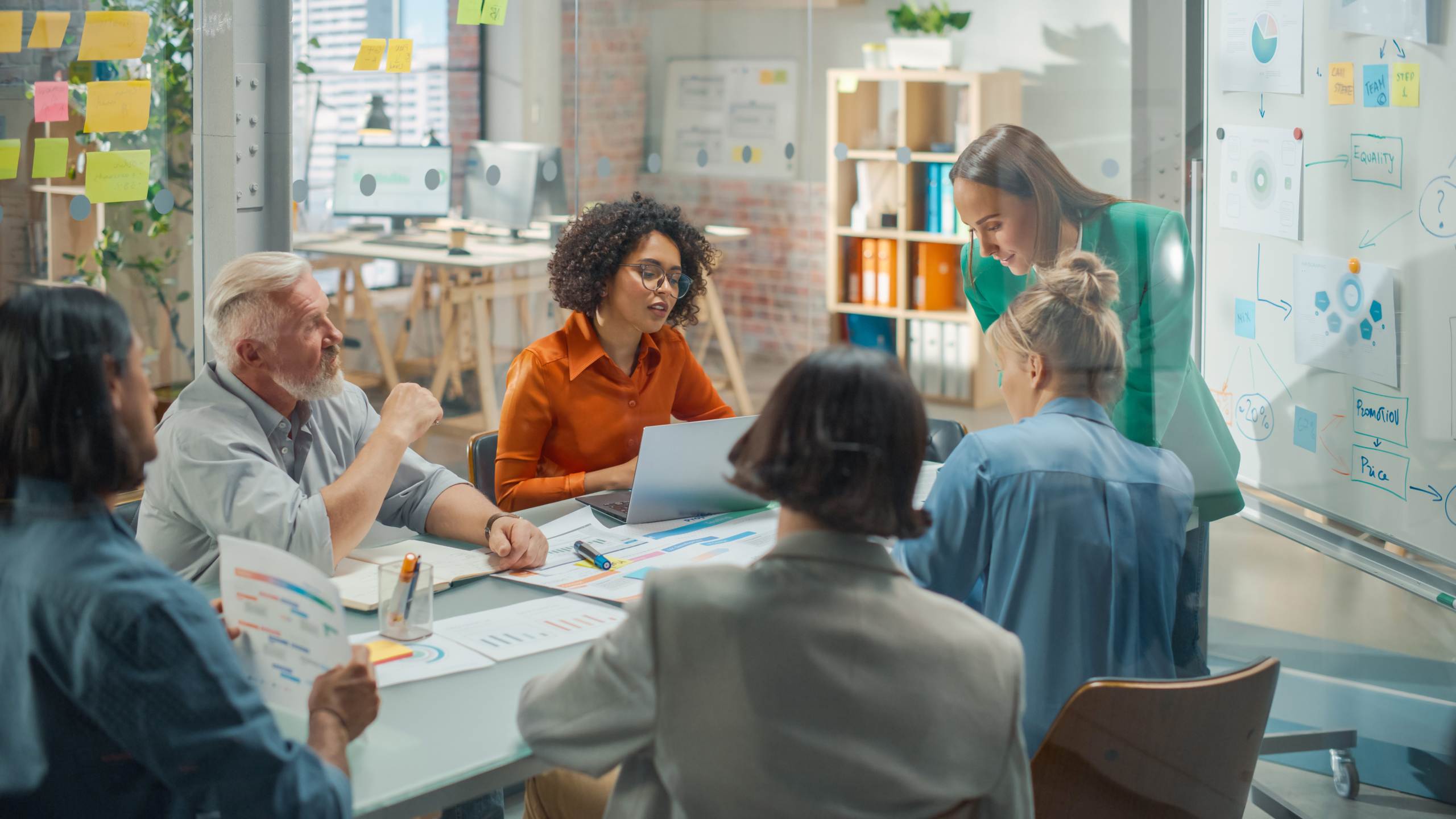
Support heavy loads easily – TX1 and TX2
Member News
iglidur tribopolymer plain bearings reduce the use of
lubricants, cutting costs and ensuring maintenance-free operation
Construction and agricultural
machinery users want to save money and significantly reduce maintenance. Dry
running iglidur plain bearings from igus are suitable for precisely these
applications.
When servicing construction and
agricultural machinery, lubricating the bearing points is one of the most
time-consuming tasks. Insufficiently lubricated and maintained bearings cause
damage to expensive shafts which can impair the function of critical machine
parts. In the worst case, there is a risk of machine failure. These failures
are costly and often occur at the most inopportune times, jeopardising
operation and project schedules. Failures and maintenance-related downtime due
to insufficient lubrication can be reduced. For metallic bearings this can be
done by central lubrication systems that continuously supply the bearing
positions with grease. However, these systems incur additional costs and
require additional maintenance, and not all bearing positions can be reached in
this way.
These lubricants are expensive
and ultimately end up in the environment. “We are talking about
significant amounts of grease that are released into the environment year after
year through lost lubrication,” explains Rob Dumayne, director of drytech
products at igus UK. Due to their familiar properties, lubricated metallic
bearings are well established in the field of high loads. Until now, there was
no way around grease – firstly, it is necessary for the bearing’s function, and
secondly it protects the shaft or moving part from corrosion. Therefore, if
switching to a lubrication-free and maintenance-free solution is to be made,
the nature of shafts and fixtures must also be factored in. Corrosion
protection waxes or nitrided (nitride coated) surfaces can be cost-effective
and efficient solutions here.
Felt as a bearing seal to retain grease
For over 30 years, igus has produced plain bearings made of self-lubricating, high-performance plastics. Solid lubricants are already incorporated into the tribopolymers. They allow construction and agricultural machinery to run free from maintenance and grease. It is important that the bearings can operate in a corrosion-free environment, because by dispensing with lubricant, the shaft and fixture are no longer protected by grease. A one-for-one replacement is therefore not possible for all bearing positions. If the shaft has to be lubricated once, igus can offer iglidur plain bearings that are manufactured with a felt seal, which ensures that the grease remains in the bearing position, i.e., it does not leak out. At the same time, the seal protects against penetration of sand and dirt. In the case of completely dry operation, the use of hard-chrome plated or nitrided surfaces is recommended.
Heavy duty= heavy load?
“Many equate heavy load with heavy-duty, however high load is only one part of heavy-duty,” says Rob Dumayne. “This term refers to particularly extreme demands on the plain bearings, that do not always have to be high loads. Moisture, dirt, shocks, vibrations or even edge loads all qualify as extreme challenges for the bearings.” For many of these special requirements, igus has developed all-rounder materials, such as the tried and tested iglidur G material, which can absorb forces of up to 80MPa. All igus materials are characterised by their dry-operating properties as well as long service life that can be calculated in advance. They are resistant to dust and dirt, making them ideal for use in construction and agricultural machinery as well as in commercial vehicles.
High-load test rig at igus@ plastic versus metal in endurance test
igus tests all its motion plastics and products in its 3,800sq m laboratory in Cologne, and has set up its own test rigs especially for high loads and certain application scenarios. These are reproduced one-to-one for load cases such as edge/impact loads. For example, there is a front loader located outdoors that moves 24 hours a day, seven days a week, in all weather conditions. A direct comparison of performance between plastic and metal bearings is also possible.
These tests allow us to determine the precise service life of the products. The test results are added to the database, and the igus online configurators predict the expected service life of the selected components.
“Tests showed that iglidur TX2 plain bearings used with hard-chromed shafts are about 3.5 times more wear-resistant than plain bearings made of iglidur TX1”
Heavy-duty bearings made from wound filament
igus has developed two plain bearing materials made of high-strength woven fabric – TX1 and TX2,. They are used where particularly high loads occur, when injection-moulded plain bearings reach their load limits. Here, the specially interwoven, extremely high tensile strength filaments ensure maximum wear resistance. “Both materials can be used to service applications where forces of up to 200MPa have to be absorbed. Deciding between the materials depends on the condition of the shaft surface,” explains Rob Dumayne. The difference between the two materials is primarily in the structure of the plain bearings that are made from them, which leads to varying wear behaviour. Both types were extensively tested on indoor and outdoor test rigs.