
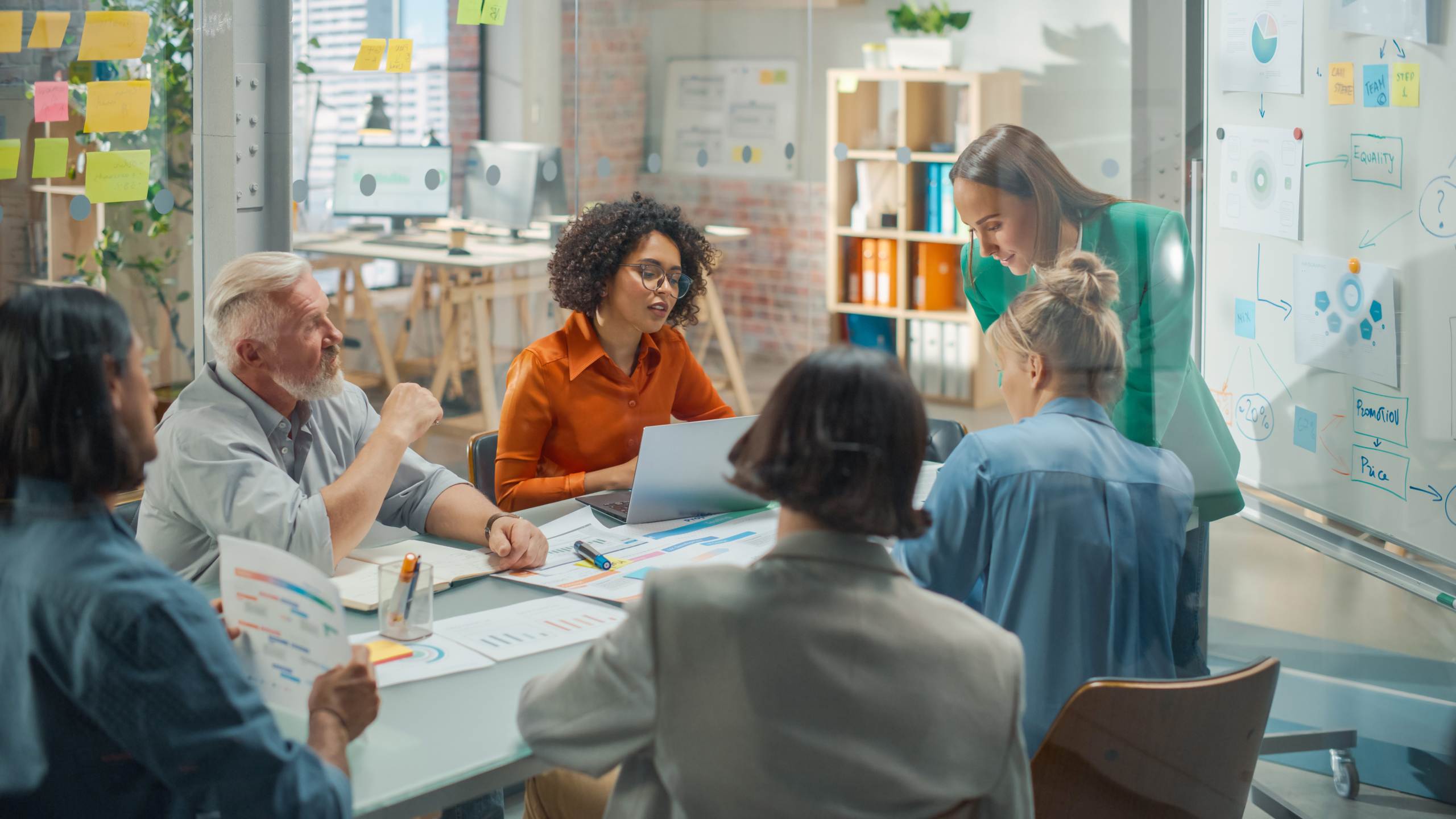
Small investment, big impact: Contactless monitoring of igus cables in e-chains
Member News
i.Sense CF.D sensors detect defects in chainflex bus and data cables,
preventing expensive
machinery downtime.
Smart monitoring of bus
and data cables from igus has entered the next phase with igus
i.Sense CF.D monitoring sensors. They check the electrical condition of chainflex cables
in e-chain systems, with no contact and without interfering with existing cable
layouts. By doing this, real-time monitoring does not require sacrificial
cables and, combined with the new i.Cee:plus II evaluator module, it enables
even more efficient predictive
maintenance to protect against cost-intensive systems failure.
The latest generation of CF.D sensors makes it easier to apply
the predictive maintenance of chainflex bus and data cables in igus
e-chain systems. The smart system consists of two sensor units that are clipped
onto the chainflex cable
to be inspected, before and after the area to be monitored. These are small
enough to fit in the distribution box on the moving side and in the control
cabinet on the fixed-point side. During operation, the sensors continuously
check the transmission properties of the cables.
High-frequency technology
detects the smallest changes in condition without contact
i.Sense CF.D, the new generation
of monitoring sensors, relies on frequency technology that works without
sacrificial cables or
contacting existing cables. “Thanks to this technology, the sensors
reliably measure even the smallest transmission deterioration of cables and
connectors,” says Justin Leonard, director of e-chains and smart plastics
at igus
UK. In this way, effective predictive maintenance is possible in moving
industrial applications in which cables and plugs are exposed to continuous
mechanical stress.
The new CF.D sensors are
compatible with most bus and data cables of the chainflex cable range
from igus.
“Thanks to condition monitoring, users of machines and systems can detect
and replace the corresponding cables that are approaching their wear limit at
an early stage, thereby significantly increasing plant safety,” Justin
adds. Thus, these sensors are a small investment with a big impact, because in
some industries downtime costs of €5,000 per minute, and more, are common.
Cee:plus II: Detecting
impending faults on smartphones and tablets
As the data and bus controls
approach their wear limit, a second system comes into play: i.Cee:plus II. A
CF.D sensor is connected via USB cable to the predictive i.Cee maintenance
module. A deterioration of the data transmission properties indicates the need
for maintenance work and adjusts the lifetime calculation of the components
used. It outputs the measurement results of each individual sensor via a
dashboard that users can access via the local network or, when mobile, on the
internet with a PC, smartphone or tablet. Thus, operators can keep up-to-date
at any time, from anywhere in the world, and can react quickly to alarm
messages received by SMS or e-mail.
The dashboard also provides an
overview of the plant’s history, including the total number of energy chain
strokes, the temperature in production and the remaining time until the next
scheduled maintenance. Justin says: “i.Cee:plus II and the new generation
of CF.D sensors together put predictive
maintenance on a secure foundation, thanks to intuitive usability
and flexible integration into the user’s IT, so that faults and unexpected
shutdowns can be prevented more reliably than ever.”
With this new generation of CF.D
monitoring modules and i.Cee:plus II, igus is
expanding the i.Sense environment for predictive
maintenance. Since 2016, the company has been developing a product
family, under the i.Sense name, in which sensors and monitoring modules make
motion plastics such as energy chains, cables, linear guides and rotary table
bearings intelligent. These smart plastics
reliably predict the service life of components in numerous customer applications,
including the automotive industry.