
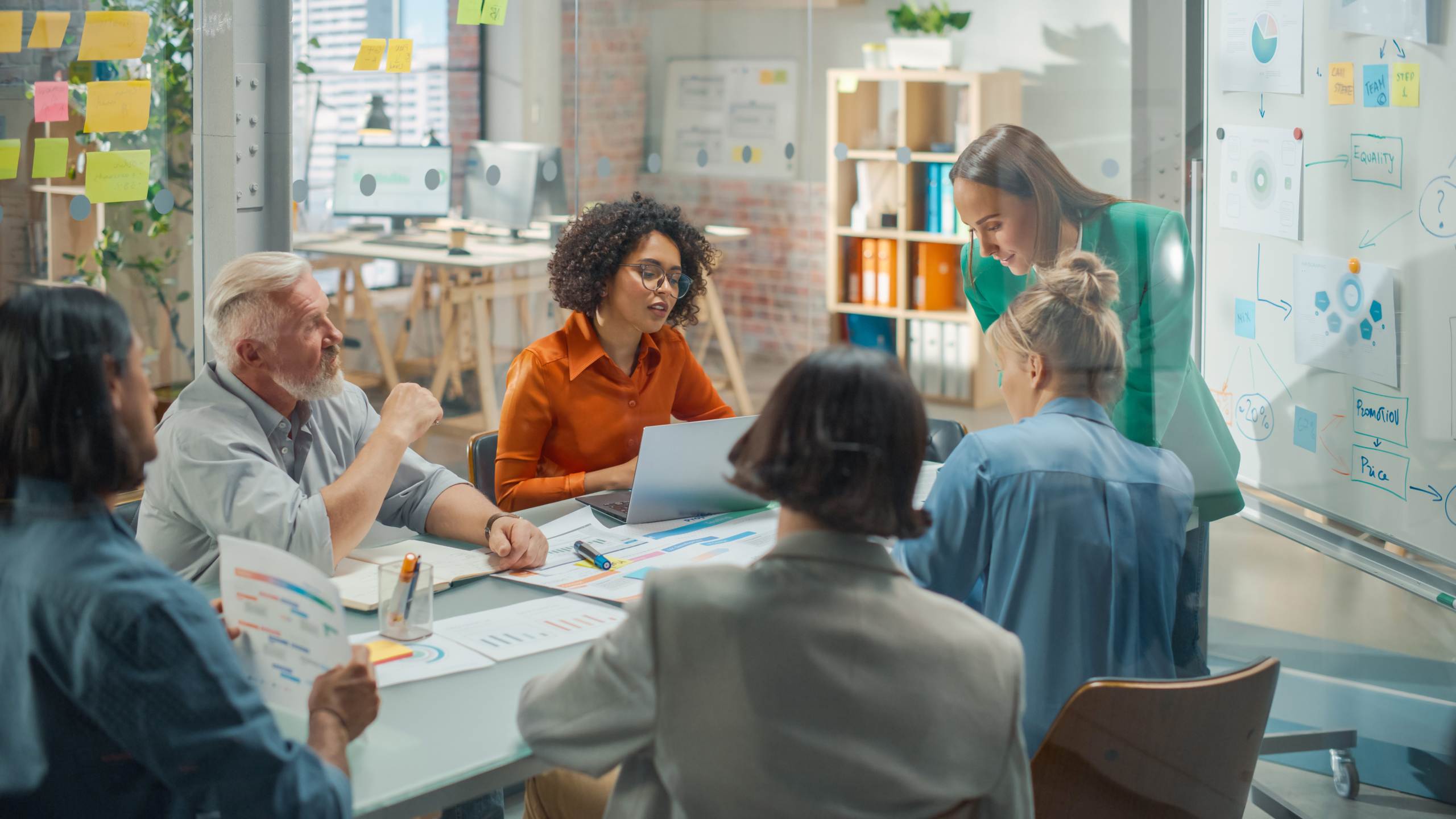
Can Plastic Injection Moulding Process be Eco Friendly?
Member News
Can Plastic Injection Moulding Process be Eco Friendly?
Plastic injection moulding might not be the first manufacturing procedure you associate with environmental friendliness. However, Great Central Plastics are taking up the reins, and leading the charge on the industry’s green credentials.
With almost a quarter of a century of experience, we are a UK industry leader in manufacturing high quality plastic injection moulded products, in-house tooling, and post-production decoration.
Something Great Central Plastics take pride in is sustainable manufacturing, and we adopt this ethos across all levels of our business. The solar panel installation generates around one-third of all our energy requirements. Also, we recycle and reprocess materials at every opportunity.
Of course, you don’t have to be a plastic moulding manufacturer to install solar panels and do some recycling. However, Great Central Plastics understand how plastic injection moulding can be eco-friendly. So, read on to find out just how.
Eco-Friendly Plastic Injection Moulding Process
Since their invention in the early 1900s, plastics have revolutionised manufacturing and practically every aspect of modern life. Indeed, they have made products cheaper and expanded the creativity boundaries of product design and production.
Unfortunately, in recent years, plastics have suffered from a bad reputation in terms of their negative impact on the environment. However, there is much being done to minimise the environmental effects of plastics and plastic product manufacturing processes.
Here’s how Great Central Plastics are making our plastic injection moulding process more eco-friendly.
Transportation
One of the most negative environmental aspects of the modern global economy is its reliance on fossil-fuelled transportation. The table below shows the top 15 plastic product exporters, by dollar value and percentage, in 2020.
Ranking |
Country |
Exported Plastics ($ Billions) |
Exported Plastics (%) |
1 |
China |
28.9 |
33.9 |
2 |
Germany |
9.5 |
11.1 |
3 |
United States |
6.6 |
7.7 |
4 |
Italy |
3.1 |
3.6 |
5 |
France |
2.8 |
3.3 |
6 |
Netherlands |
2.35 |
2.7 |
7 |
Poland |
2.34 |
2.5 |
8 |
Japan |
2.1 |
2.4 |
9 |
Mexico |
2 |
2.3 |
10 |
Taiwan |
1.84 |
2.2 |
11 |
Czech Republic |
1.82 |
2.1 |
12 |
Hong Kong |
1.7 |
2 |
13 |
South Korea |
1.5 |
1.8 |
14 |
United Kingdom |
1.3 |
1.6 |
15 |
Austria |
1.2 |
1.5 |
Source: https://www.worldstopexports.com/plastic-item-exports-country/ accessed 22/6/22
You will notice that the United Kingdom lies in 14th place, meaning we import much of our plastic products from far off places such as China. Have you considered the environmental cost of transporting these goods from the other side of the globe? Let’s take a look at what it costs us in environmental terms.
The table below details the amount of CO2 (in grams) emitted for one metric ton of freight moved 1km:
Transportation Method |
CO2 Emissions (g/ton/km) |
Air Cargo – Boeing 747 |
500 |
Modern Lorry |
60-150 |
Modern Train |
30-100 |
Ship |
10-40 |
Source: https://timeforchange.org/co2-emissions-for-shipping-of-goods/ accessed 22/6/22
What do these figures mean in practical terms? For instance, moving one ton of plastic products from Shanghai to London by sea. The distance between the two ports is 11,866 nautical miles, or 21,976 km. That means it is costing between 220 – 879 kg in CO2 emissions.
Compare that to moving the same one ton of plastic products to London from Great Central Plastics in Northamptonshire, a road journey of around 123 km. The CO2 emission cost now is drastically reduced to between 7.38 – 18.45 kg.
Materials
When it comes to materials, Great Central Plastics is innovating to minimise our environmental impact. We manufacture no single-use products, meaning that the goods we supply have long-term utility.
We also use various eco-friendly and bio-based plastic materials, such as PLA. Of course, there are situations where traditional petroleum-based plastics are required, but often these greener materials are more suitable.
Some of the recycled and plant-based plastic options Great Central Plastics offer include the following:
- Recycled White Goods
- Styrolux
- Recycled PPCP
- Recycled Styrene
- Recycled ABS
- Terralene
- Terraprene
- Bio Flex
Energy Source
Energy is a crucial factor for all companies, and Great Central Plastics are doing our bit to keep our energy consumption as green as possible. However, before you see what we are doing, let’s put plastic injection moulding’s energy usage in context.
Here are the top ten energy consumers by sector:
Ranking |
Sector |
KTOE (kilotonne of oil equivalent) |
1 |
Private Offices |
3,539 |
2 |
Chemical Manufacturing |
2,874 |
3 |
Hospitality |
2,458 |
4 |
Food Manufacturing |
2,242 |
5 |
Hospitals |
2,237 |
6 |
Non-Metallic Mineral Manufacturing |
1,924 |
7 |
Basic Metals Manufacturing |
1,489 |
8 |
Rubber and Plastic Manufacturing |
1,442 |
9 |
Small Shops |
1,376 |
10 |
Paper Products Manufacturing |
1,297 |
Source: https://www.tariff.com/news-and-insights/which-uk-sectors-use-the-most-energy/ accessed 22/6/22
As you can see, plastic injection moulding sits well below most sectors for energy consumption. Still, Great Central Plastics are striving to make our sector as eco-friendly as possible. We’ve installed solar panels at our Northamptonshire manufacturing facility. Consequently, one third of all our energy is generated by the sun.
Conclusion
At first glance, it might be easy to decry plastic and its associated industries as being damaging to the environment. However, when you delve into the issue, you can see there is a lot that can be done to make these manufacturing processes more eco friendly.
Great Central Plastics are doing just this through CO2 reductions in transportation, innovative use of materials, and using renewable energy sources. Perhaps the question should not be “can the plastic injection moulding process be eco friendly,” but why are other sectors not following such a shining example?