
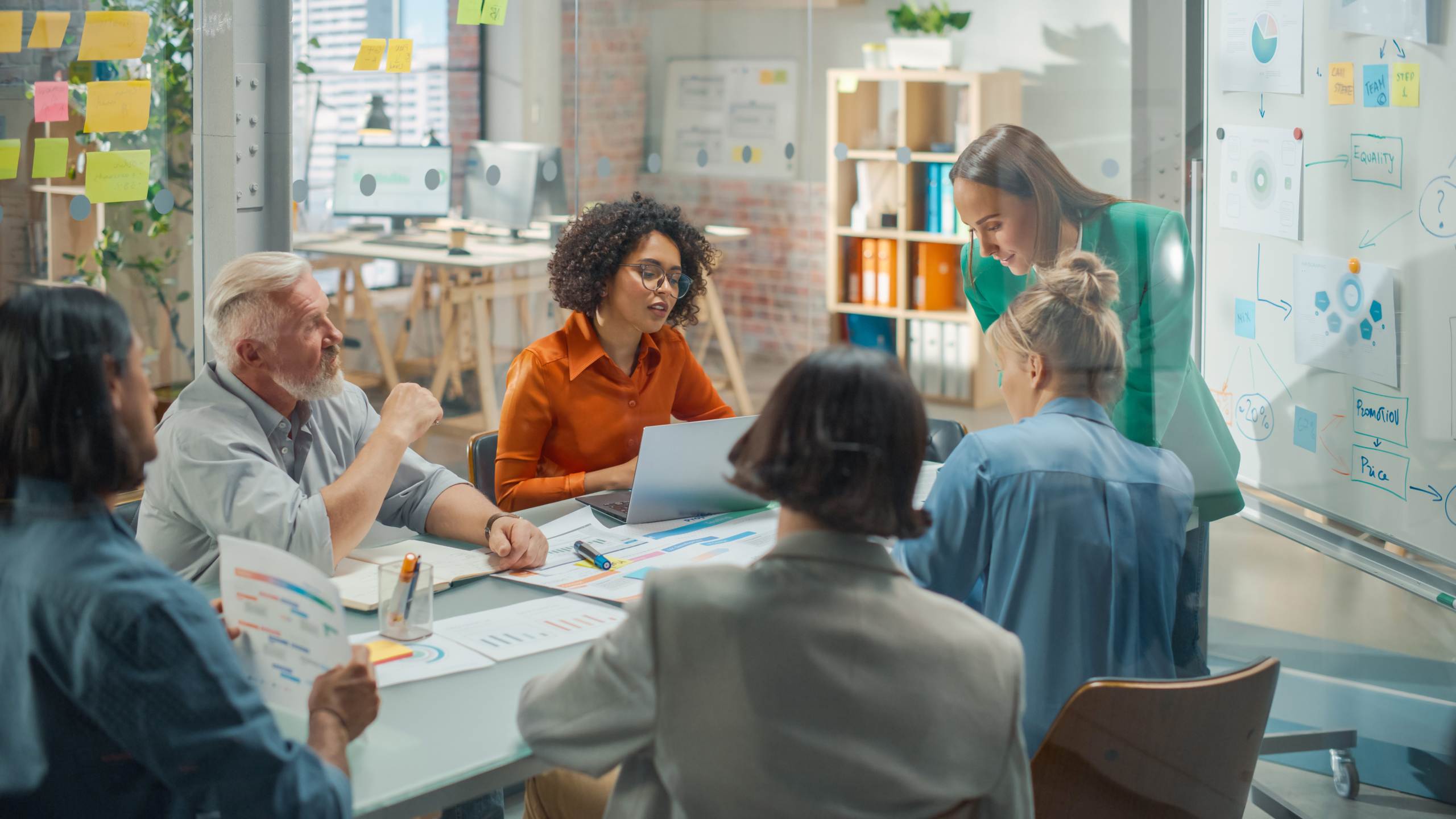
Autonomous cleaning robot runs even cleaner with drylin linear bearings
Member News
Lubrication-free drylin linear guides ensure smooth operation of
the K900 cleaning robot from KEMARO AG
The K900 industrial robot cleans
floors wherever it needs to, autonomously and without programming, even in
places where it is potentially dangerous or even impossible for people to
clean. Lubrication-free linear guides, shafts, plain and fixed flange bearings
from igus
all play a crucial role in the robot’s mechanics.
Three Swiss engineers; Armin
Koller, Thomas Oberholzer and Martin Gadient, founded KEMARO AG in August
2016 to develop autonomous robots. With the K800, the young company from Eschlikon,
Thurgau launched the world’s first autonomous dry-cleaning robot for industrial
use. “We wanted to develop a product that the world needed, was
technically mature, improved the cleaning process and helped save money and
time – thus the idea of an industrial cleaning robot was born”, says
Martin Gadient, co-founder of KEMARO AG and in charge of the Mechanics
& Production division. The 13-person company launched the successor model
K900 in 2020.
Plug in, load and clean
Whether it’s a warehouse, production
facility or industrial plant, the K900 cleans without chemicals or water,
leaving the floor clean and – crucially – dry. Due to its low installation
height, the robot cleans even in places that are hard to reach or potentially
dangerous for people to access. Commissioning is very easy and fast and
requires little or no preparation time or programming.
The user simply places the K900
in the desired location, plugs it in, charges it and the autonomous cleaning
can begin.
“Companies save massive
cleaning costs with a K900,” says Gadient. “They also protect the health of
employees by reducing fine-dust pollution and dispensing with chemical cleaning
agents. Another plus is that a cleaning robot allows the workforce to
concentrate fully on their value-adding activities again”.
The sweeping robot is designed
for cleaning areas up to 10,000m2. It has a battery run time of up to five
hours, an integrated dust extraction system, a cleaning width of 90cm and a
dirt container with a capacity of 35 litres. “As it travels, our
robot creates its own cleaning map, identifies and bypasses fixed and mobile
objects, and cleans its environment completely independently,” says Gadient.
“In the case of cleaning robots for industry, we are currently the only company
in the global market that can simply place the robot in a room and start it at
the push of a button. There is no need for prior space measurement or
teach-in”, the co-founder adds. To make the robot mobile, it has a trolley
handle that is guided cleanly, strongly and safely with a drylin T
linear guide from igus.
Lubrication-free and maintenance-free linear guides made to measure
Martin adds: “From my past work as a development engineer, I already knew the products from igus, and my experiences with them had always been good. For our size and the confined space conditions, we needed a strong and robust linear guide that was made-to-measure. We contacted igus and a short time later, we ordered a sample of the desired linear guide for testing from their website”. Axel Ebert, Key Account Manager Bearing Technology at igus
Switzerland, adds: “You can easily order a sample guide from us via our website – also made-to-measure from customer drawings. Due to the required strength, we decided on a drylin T linear guide in HD (heavy-duty) version in coordination with KEMARO AG.”
Profile guides of the drylin T type are dimensionally identical to the usual lubricated ball guides. In contrast, noise is reduced with the drylin t guides, as is the surface pressure due to the larger contact surface between the guide and the profile rail. In the heavy-duty version, the slides have a very firm hold in the carriage body. The drylin T carriage guides can handle loads up to 14,000N, are extremely resistant to dirt and have a very long service life. “That’s another advantage of igus products – they’re all lubrication-free and therefore ideal for our application. The customer never has to lubricate, so no dust sticks to the guides and no abrasive paste can form”, says Gadient. Aluminium is used for the shaft material. “At first we had a chrome steel shaft that we kept having problems with,” says Gadient. “Axel Ebert then suggested an aluminium shaft from the igus portfolio.
Initially I was very sceptical,
but after the first test I was completely thrilled. It is both lighter and also
easier to assemble and works perfectly”. For more lubricant-free benefits:
in addition to the carriage guidance, the fixed flange bearings,
plain bearings
and thrust washers
from igus are also used in the robot.
“Our igubal spherical
bearings, which are used in the roller brush bearing, are
maintenance-free, self-aligning bearing elements made entirely of plastic. In
addition, the entire igubal joint system is insensitive to dust and dirt,
resistant to corrosion, and 80% lighter than metal bearings”, says Daniel
Henlin, Sales Manager at igus
Switzerland, emphasising the advantages of spherical bearings made of
high-performance plastics.
Conclusion
By using the igus
lubrication-free bearing technology, the directors at KEMARO AG were able
to make their autonomous sweeping robot quieter, more robust, lighter and also
more durable. And it also requires less maintenance. “The collaboration
with igus is as we hoped – the advice is top class and the price-performance
ratio is right. But above all, the quality of the product is convincing, and
this in turn increases the quality of our product”, concludes Martin
Gadient.