
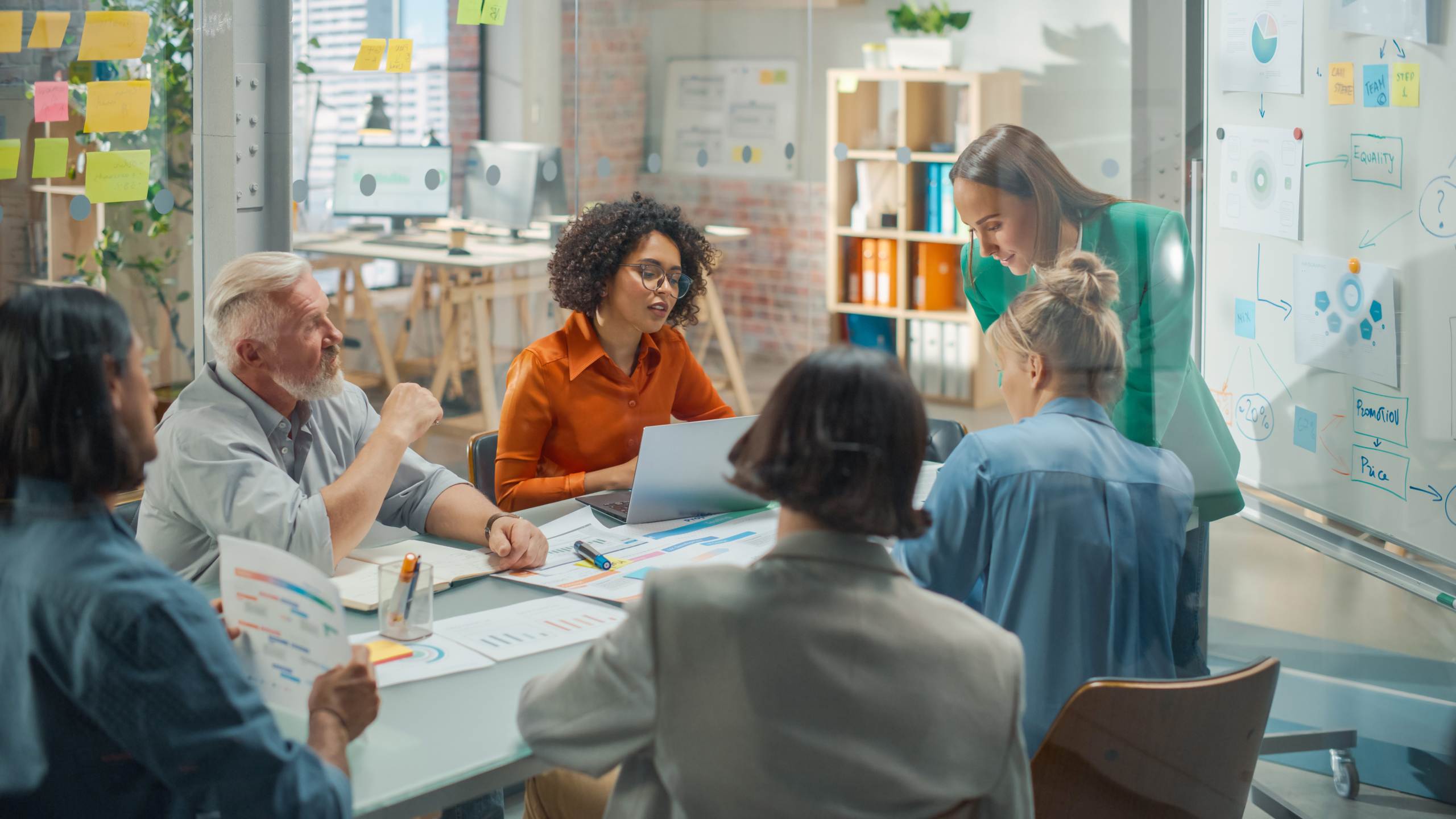
When did you last test your company equipment?
Blogs
CRYSTAL CLEAR COMPLIANCE – SEPTEMBER 2020 BLOG
When did you last test your company equipment?
By Lucy Walsh
Employee safety is high on every company’s agenda right now, for obvious reasons.
But, whilst employers and health and safety officers have been busy making workplaces COVID secure and taking all the necessary steps to ensure the safety of staff at home and returning to work, other jobs that are usually taken care of as a matter of course may have fallen through the cracks.
One of these is the routine testing and maintenance of electrical, plant and other equipment.
It is quite feasible that with many people away from the workplace for months on end, if these tests and checks were due to be carried out during lockdown, they may have been forgotten or pushed back due to the prioritisation of other things or costs.
The importance of regularly testing and maintaining equipment cannot be underestimated. They are key to ensuring the safety of people and the building.
Electrical safety
Where equipment has been left in unmanned workplaces, sitting idle for weeks or even months, it is only sensible to ensure it is still safe to use and the easiest way to do this is to have it tested. For example, if your workplace’s electrical system has been operating on a reduced load in recent months it would be a good idea to ask a qualified electrician to restore loads slowly. By doing this you will prevent damage to your electrical systems.
Testing could include calibration testing, Portable Appliance Testing (PAT testing) and the five-year electrical test which applies to commercial, office, retail and educational properties.
Don’t forget that maintaining your electrical systems will also be a vital element of your insurance policy. It is also necessary to ensure you are up to date with the relevant health and safety regulations.
Water hygiene
Another important area to consider is water hygiene. It’s essential that systems are flushed through before you allow staff to use them. If there is stagnant water in the systems, this can pose a risk of legionella which is the bacterium which causes legionnaires’ disease.
The Government and HSE has released a lot of information on this topic as has the Legionella Control Association (LCA). The LCA has produced a helpful guide to show firms how to minimise the risks associated with legionella bacteria in water systems post a COVID-19 shutdown. In the LCA’s view simply reopening a building that has stood idle, without addressing the safety of its water system, is unacceptable and is likely to be in breach of the law. It states if dutyholders are not able to put in place a proper recommissioning process to use the water system safely, they should not reopen their building.
Emergency facilities
Finally, don’t forget to make sure your emergency facilities are up to date and operational. Ensure that you have checked fire detection, alarm systems, sprinkler systems and emergency lighting are working correctly. Remember to ensure that fire doors are not blocked and can still be opened.
PUWER
It is also incredibly important to be aware of the Provision and Use of Work Equipment Regulations 1998, commonly abbreviated to PUWER 1998 or simply PUWER. These regulations place duties on people and companies who own, operate or have control over work equipment. PUWER also places responsibilities on businesses and organisations whose employees use work equipment, whether owned by them or not.
PUWER requires that equipment provided for use at work is:
• suitable for the intended use
• safe for use, maintained in a safe condition and inspected to ensure it is correctly installed and does not subsequently deteriorate
• used only by people who have received adequate information, instruction and training
• accompanied by suitable health and safety measures, such as protective devices and controls
• used in accordance with specific requirements, for mobile work equipment and power presses
Some work equipment is subject to other health and safety legislation in addition to PUWER. For example, lifting equipment must also meet the requirements of LOLER, pressure equipment must meet the Pressure Systems Safety Regulations and personal protective equipment (PPE) must meet the PPE Regulations (PDF)- Portable Document Format.
If you need further support and guidance on how to manage workplace health and safety during this time, or want Crystal Clear Compliance’s help with testing requirements, contact Lucy Walsh at Crystal Clear Compliance on 07748 860076 / 01536 770249 or email maito:lwalsh@crystalclearcompliance.co.uk
You can also subscribe to receive an email alert whenever a new blog is published here.