
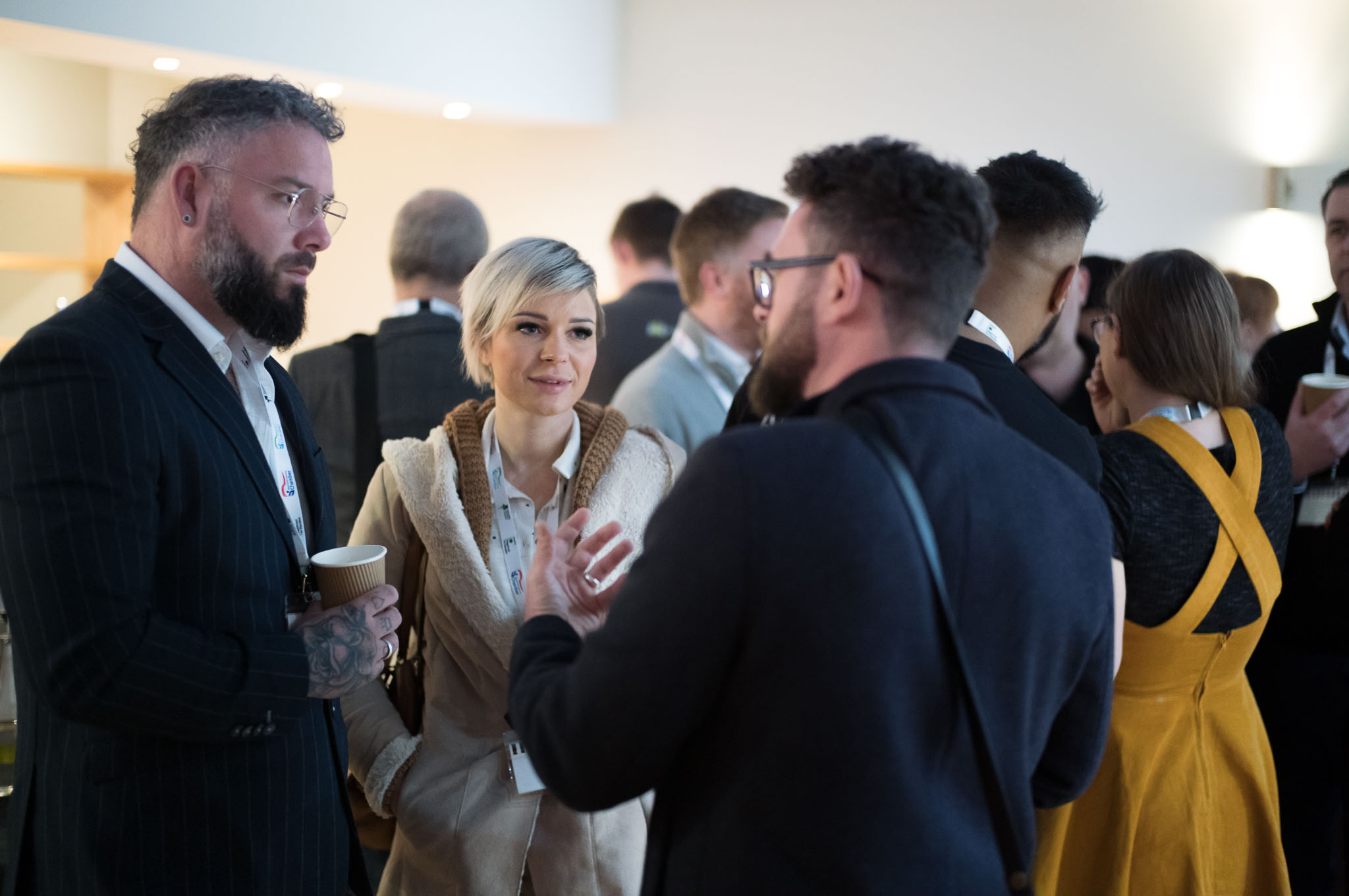
Lessons Learned: Navigating Extensive Delays in Construction Projects
In the construction industry, delays can snowball into costly, reputation-damaging crises if not managed effectively. A recent project I encountered—marked by extensive delays, subcontractor insolvencies, procurement inefficiencies, and poor coordination—provides valuable lessons on how to prevent and address such issues. This article examines these challenges, offers insights from UK construction law, and outlines corrective steps to mitigate future risks.
The Scenario
Key issues contributing to delays included:
1. Subcontractor Insolvencies: Multiple subcontractors went into liquidation during the project, causing significant disruption.
2. Procurement Delays: A lack of urgency in securing contracts led to delayed material deliveries and uncoordinated schedules.
3. Unprepared Site Conditions: The MEP contractor started work on a soft-start basis as the floor plates were not fully ready, leading to inefficiencies and rework.
4. Poor Coordination: Miscommunication between teams caused resource bottlenecks and sequencing issues.
Lessons Learned
1. Subcontractor Insolvencies:
· UK Construction Law Insight: Under the Housing Grants, Construction and Regeneration Act 1996 (as amended), contractors can mitigate risks through robust payment mechanisms and regular financial assessments of subcontractors.
· Corrective Steps:
o Conduct thorough financial due diligence before onboarding subcontractors.
o Maintain a pool of pre-qualified backup subcontractors to replace insolvent ones quickly.
o Use performance bonds or parent company guarantees to safeguard against insolvencies.
2. Procurement Delays:
· UK Construction Law Insight: Delays in procurement may constitute breaches of contract if they prevent timely completion. Contracts must clearly define procurement timelines.
· Corrective Steps:
o Establish a procurement strategy with defined milestones and accountability.
o Use collaborative contracts like NEC to promote early involvement of all parties.
o Regularly review procurement progress in project meetings to flag potential delays early.
3. Unprepared Site Conditions:
· UK Construction Law Insight: Delays caused by unready site conditions can lead to claims for extensions of time and additional costs under JCT and NEC contracts.
· Corrective Steps:
o Conduct detailed pre-construction planning to ensure site readiness before any contractor mobilizes.
o Implement a phased handover strategy to align site readiness with contractor requirements.
o Include clear soft-start provisions in contracts to outline expectations and compensation.
4. Poor Coordination:
· UK Construction Law Insight: Under NEC contracts, lack of coordination could be addressed through early warning systems and regular programme reviews.
· Corrective Steps:
o Appoint a dedicated project coordinator to oversee communication and sequencing.
o Use digital tools like Building Information Modelling (BIM) to enhance coordination and clash detection.
o Establish weekly coordination meetings with all stakeholders to align schedules and resolve conflicts proactively.
Preventative Measures for Future Projects
To avoid repeating these mistakes, consider the following steps:
1. Robust Pre-Planning:
· Develop a detailed project programme with clearly defined milestones, critical path activities, and risk contingencies.
· Include a detailed MEP integration plan to ensure readiness for contractors.
2. Contractual Safeguards:
· Use contracts that encourage collaboration, like NEC, to foster early warning systems and risk-sharing mechanisms.
· Include clear clauses on delays, extensions of time, and liquidated damages to manage expectations.
3. Financial Monitoring:
· Regularly assess the financial health of subcontractors throughout the project lifecycle.
· Implement real-time payment tracking to identify and resolve financial stress early.
4. Digital Solutions:
· Leverage project management software for real-time updates and enhanced communication.
· Utilize BIM to improve coordination, sequencing, and clash detection.
Final Thoughts
Delays are inevitable in construction, but their impact can be minimized through proactive planning, effective coordination, and contractual clarity. By learning from past challenges and integrating these lessons into future projects, we can build a more resilient and efficient construction industry.
Have you faced similar challenges in your projects? Share your experiences and insights in the comments. Together, we can drive meaningful change in the way we approach construction project management