
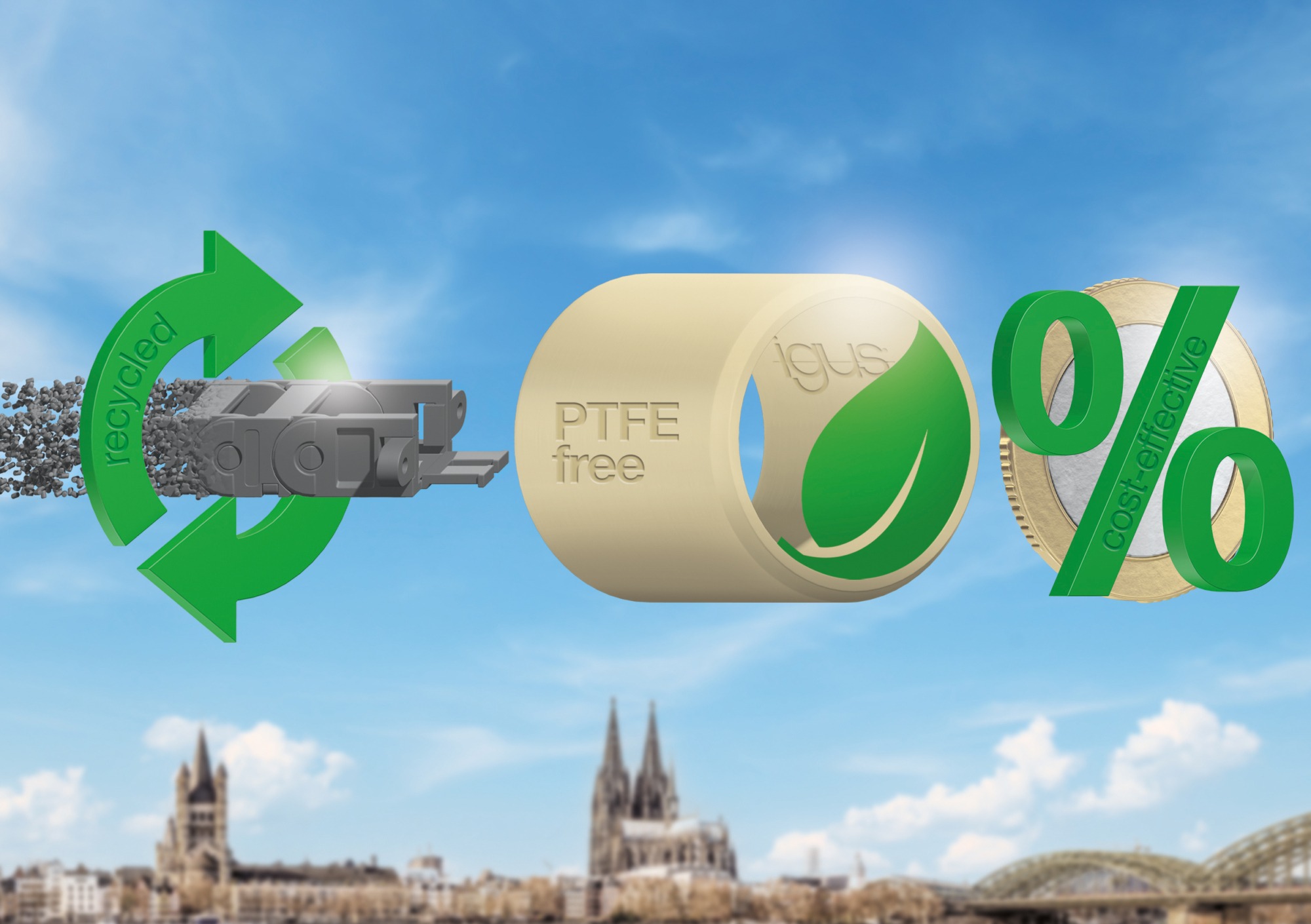
Cost-saving sustainability: PTFE-free solutions for the industries of tomorrow
igus is proud to showcase PTFE-free materials and a complete energy chain series made of recycled material.
Motion plastics specialist igus latest product developments demonstrate the newest sustainable and low carbon innovations, from PTFE-free materials to a complete energy chain series made of recycled material – plus the dry cleanroom certificate for igus e-chains, developed in collaboration with research group Fraunhofer IPA.
With uncertainty in global markets and rising political tensions, companies are facing huge challenges, often opting to save rather than spend. But companies also need to act when it comes to sustainability. “The way we live and work is constantly changing. That’s why we see ever-changing conditions as an opportunity to improve,” says Rob Dumayne, drytech director at igus UK. “This complex environment is a chance for us to take a different approach and develop innovative solutions for our customers.”
Matthew Aldridge, managing director at igus in Northampton, adds: “We want to offer solutions that make our customers more competitive and provide sustainable solutions with real benefits, without compromising on quality.” Both machine manufacturers and their customers therefore benefit from the advantages of high-performance plastics, as they don’t require any lubrication or grease, which protects the environment and saves costs and maintenance. Reducing the use of PTFE materials in industry is an important part of this.
Goodbye PTFE
One sustainability challenge that will affect many companies is the future use of polytetrafluoroethylene (PTFE), currently under regulatory review for restricted use or a formal ban. Regardless of whether there will be a ban, igus has been researching PTFE alternatives for several years. “We are working hard here, developing new formulations, carrying out extensive tests, we also test our materials for PFAS compounds (a PTFE derivative), and we adapt our production processes to offer our customers a suitable solution in the future,” says Dumayne.
igus is now offering options for all iglidur standard materials as PTFE-free variants. igus also offers PTFE-free and PFAS-tested alternatives in other product areas such as linear guides, slewing ring bearings and bearing liners. Tests in the company’s in-house laboratory for friction and wear behaviour also show that materials with substituted PTFE, compared to the PTFE-containing material, perform significantly better.
80% CO2 saved: The recycled e-chain series
Following the success of the first energy chain made from recycled material in 2022, igus has now converted its entire catalogue range of the standard E2.1 energy chain series to the new recycled material igumid CG LW, a product that is made from end-of-life energy chains recycled through the company’s own “chainge” program. “With this recycled chain series, our customers can make a contribution to the circular economy for plastics together with us,” says Matthew Aldridge. “And it also proves that sustainability doesn’t have to mean expensive, because the recycled E2.1 series are available at the same price as the e-chains made of standard material.” It also has identical mechanical properties, and an 80% lower CO2 footprint compared to the standard energy chain series.
New technologies for the industries of tomorrow
In addition to working for a more sustainable future for engineering plastics, igus is also driving the development of innovative solutions and certifications for special areas of plastics application, like dry cleanrooms for battery production. The demand for lithium-ion batteries for electric cars is increasing, bringing with it demanding production environments. “In battery dry cleanrooms, many systems break down quickly and have to be replaced after two or three months,” says Matthew Aldridge. Two years ago, igus presented the E6.29, the first certified energy chain for dry cleanrooms. Together with research institute Fraunhofer IPA, the company has now developed a new type of certificate that confirms the cleanroom suitability of igus e-chains in long term tests. Even after 15 million double strokes, or 10 months, the e-skin soft SKS28 still achieved ISO class 4 – the best possible certification. The E6 has also proven itself in long tests and was upgraded from ISO class 4 to 5. At the same time, the company is researching and developing many other progressive technologies, from low-cost automation solutions such as AGVs for intralogistics to the world’s first mobile shore power connection system for container ships.
For more information on this product, please contact:
Taylor Macdonald
Tel: 01604 677240
Email: tmacdonald@igus.net