
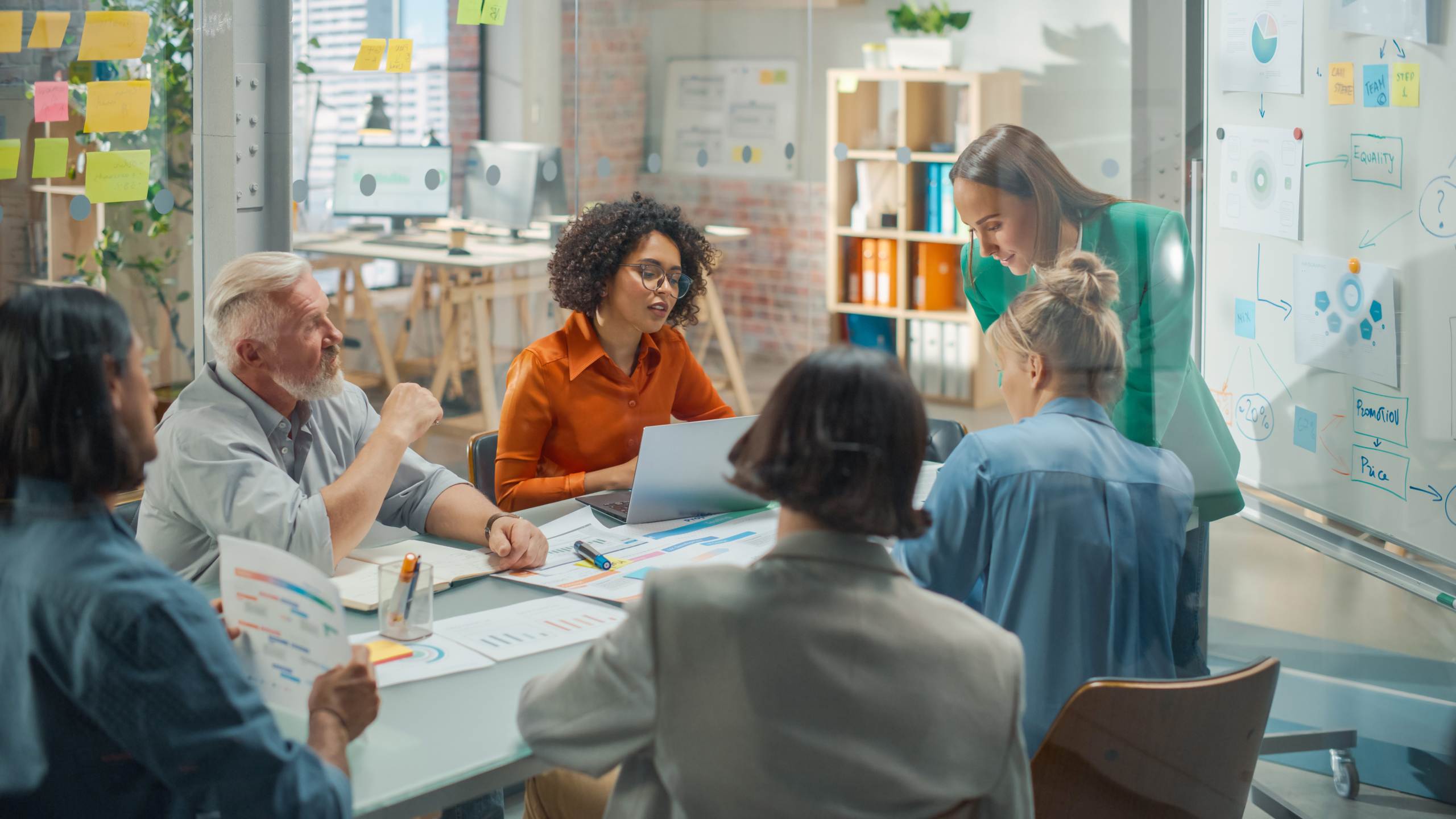
Case study : Project – Can-buddy®
Blogs
Project: Can-buddy®
Quantity produced: 5,000
What inspired your project?
The idea for Can-buddy® came about after a wasp flew into the opened can of cola I was enjoying with my lunch. Luckily, I saw this so it ended up in the bin – a wasp sting in the mouth or throat could have been very nasty indeed! To prevent this from ever happening again I would stuff a tissue in the opened can I was drinking from, but this often resulted in soggy tissues, which was rather unpleasant so I looked for alternatives. I didn’t find any products I liked, something which was both functional, cute and would cover my opened cans and so the idea for me to develop Can-buddy® was born!
What challenges did you face?
My first challenge was designing a prototype of the idea I had in mind for Can-buddy®. I initially designed the prototype using modelling clay and tested this on a variety of different sized drinks cans from small mixer size cans to large beer cans to make sure the design would fit all the different can sizes drinks are available in. The next challenge was investigating how and where I could manufacture Can-buddies on a large scale, what type of material they could be made from and most importantly where could I find a UK manufacturer to help me with all these questions! Many hours were spent on the internet researching how I would go about making the Can-buddies into a well-designed, useful product. From my research it looked like plastic injection moulding would be the best way to produce my Can-buddies and this is when I discovered the website of Great Central Plastics (GCP) who design and produce bespoke plastic moulded products. I thought they would be an ideal company to approach with my idea, especially as the company is based in the UK, making communication easier.
How did GCP help overcome your challenges?
I contacted GCP, showed them my modelling clay prototype Can-buddy® and enquired if they could help me make it into a viable injection moulded product. I was delighted when they said they liked my idea and would like to work with me to develop Can-buddy®. GCP advised me on the design – the initial prototype was rather portly, so I was advised it would be better to be slimmed down otherwise the product could end up distorted when they came out of the injection mould and dried – not a good look for Can-buddy®! I also wanted the can cover part and the figurine part of Can-buddy® to be one whole unit rather than having two separate parts so GCP helped develop CAD which would both work in the way I had intended and also be suitable for production via plastic injection moulding. The next step was GCP using the CAD to do a 3D print of the Can-buddy® design and test this on a variety of drinks cans. This 3D printed model worked perfectly and the next step was GCP producing the injection mould tool for the plastic injection moulding of Can-buddy® and me deciding what colours in which to produce the can-buddies. Throughout this project, GCP have been extremely helpful in answering my many queries and guiding me through the complexities of making my Can-buddy® idea a reality.