
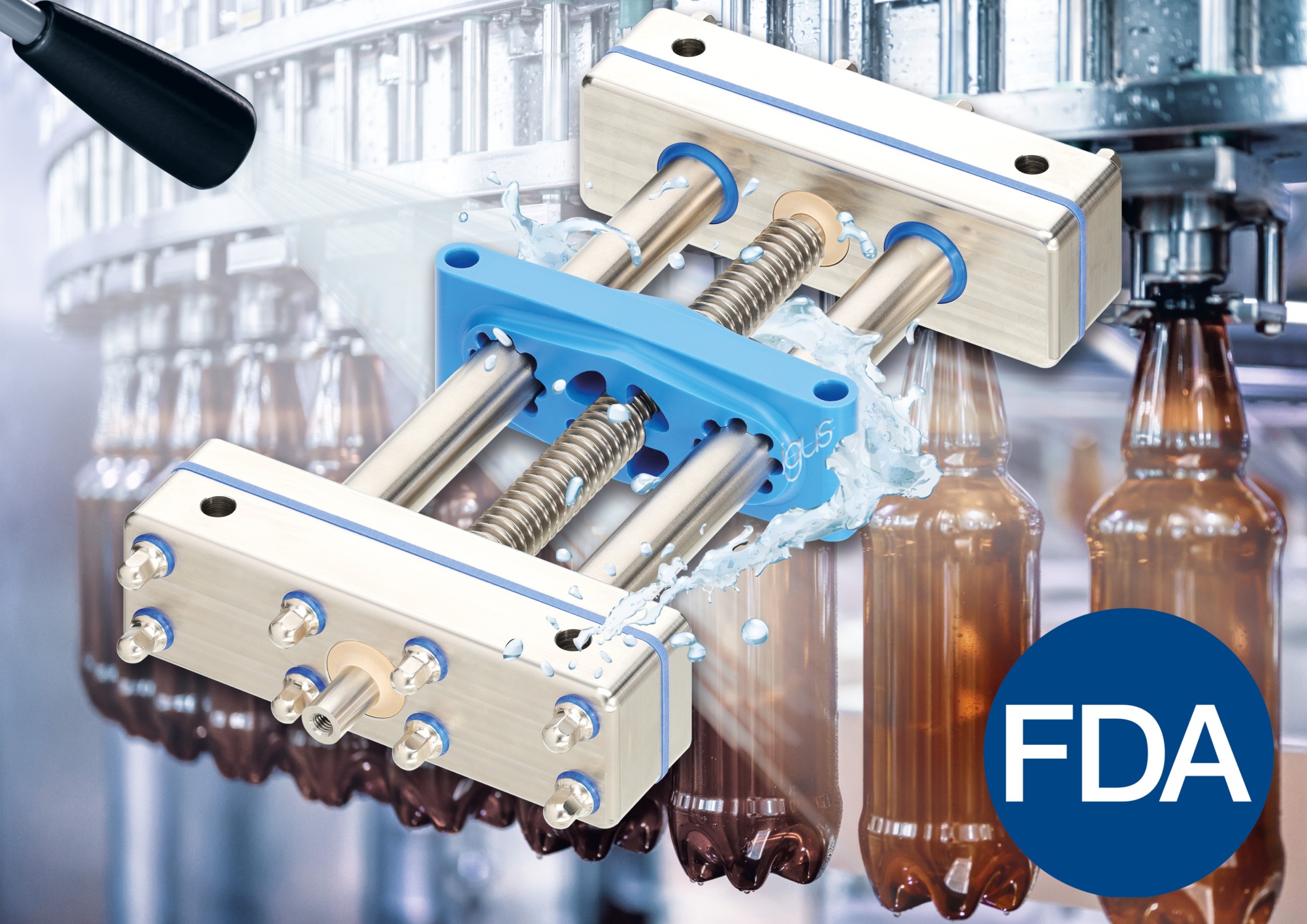
Raising hygiene standards for drinks manufacturers: hygienic SHT linear module
Raising hygiene standards for drinks manufacturers: hygienic SHT linear module
igus presents lubrication-free drylin linear and drive technology – designed according to EHEDG guidelines.
There is an increasing pressure for drinks companies to manufacture more hygienically. Consumer demands for product safety are growing, and global standards from authorities such as the Food and Drug Administration (FDA) are becoming stricter, meaning the demands on machine components are also increasing. To enable machine builders and operators to achieve hygienic, low-maintenance, and fail-safe production, igus® has designed lubrication-free drylin® linear and drive technology, that includes a design study for a ready-to-install SHT linear unit. The design not only meets FDA and EU requirements but also the cleanliness guidelines of the European Hygienic Engineering Design Group (EHEDG).
With stricter regulations, companies in the beverage industry must ensure that their systems for filling, labelling, packaging, and inspecting bottles and cans are easy to clean. This also applies to machine components, such as linear technology used for adjusting and moving filling heads, label dispensers, and camera systems. “Demand for linear technology with hygienic design is increasing rapidly,” says Rob Dumayne, drytech director at igus® UK.
“Machine manufacturers are looking for ways to further reduce contamination risks in their systems and at the same time reduce the cleaning effort and operating costs that come with this.”
To meet these needs, igus® presented a large product portfolio at the beverage industry’s BrauBeviale 2024, that are developed to meet the guidelines of the European Hygienic Engineering & Design Group (EHEDG). These require that components are either free from crevices and gaps design or be sealed appropriately. “This allows us to support the safe and efficient operation of production facilities in the beverage industry,” says Dumayne.
SHT Linear Module for hygienic positioning tasks
Among the many innovations shown was the design study of a ready-to-install SHT linear unit in a hygienic design, optimised for better cleaning and wash-down. The SHT unit can be used for filling stations to enable precise and hygienic movements for the positioning of bottles and cans. The linear module has stainless steel round shafts as guides and is driven by a dryspin® thread from igus® made of corrosion-resistant stainless steel. The support assembly consists of two housing halves sealed with an FDA-compliant silicone flat gasket and hygienic screws. Specially designed wiper seals protect the shafts and prevent dirt and moisture from entering the support unit.
Additionally, igus® has designed the threaded nut on the dryspin® screw to create generous gaps, preventing deposits and enabling efficient cleaning. “We are developing more and more products that comply with the hygienic design guidelines and have now also joined the EHEDG to jointly enable certifications for igus moving parts,” says Rob Dumayne.
Growing portfolio of hygienic designs has many applications
igus® had presented the world’s first slide for linear guides with hygienic design in 2023, made of 100% food-compliant plastic with FDA and EU 10/2011 approval. Here also, the design is completely open, making the system fully flushable – even with the use of aggressive cleaning agents. The carriage is suitable for adjustment in beverage filling systems to handle different bottle sizes without interchangeable parts.
Thanks to solid lubricants integrated into the high-performance plastic, the carriage allows hygienic and low-maintenance dry running without external lubrication. The drylin® Hygienic Design portfolio now also includes individual bearings that are located separately on the guide rail and are assembled into linear slides by stainless steel plates of various sizes to allow for a more flexible design. This also includes the drylin® ZLW timing belt linear unit made of stainless steel with bearing points, timing belts, and ball bearings made of FDA and EU 10/2011-compliant plastic.
These igus® components have already proven themselves in a wide range of applications in the food, beverage, and packaging industries: from Krones AG’s inspection technology to the robot kitchen from the start-up Cook-e and the fully automatic pizza oven from BistroBox! Dumayne says, “Thanks to its hygienic design and easy cleaning, our linear and drive technology meets the strict requirements of the beverage and food industry, contributing to safety and efficiency in the production process.”
For more information on this product, please contact:
Taylor Macdonald
Tel: 01604 677240
Email: tmacdonald@igus.net